To make my hand-shaped five-sensor E-Textile I have been applying the knowledge from making one E-Textile pressure sensor. It more or less worked in the same way but just posed more challenges aligning the fabric than when it was only 1 sensor.
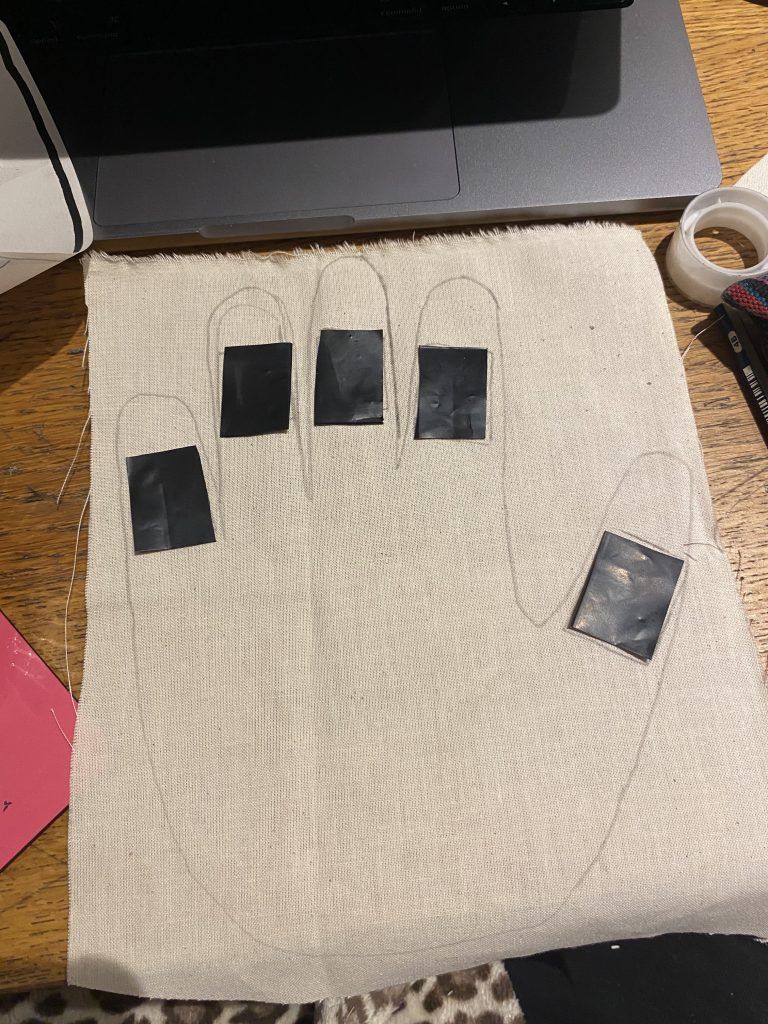
First I drew the outline of the hand shape onto my fabric. In the next rendition of the hand, I will make it a little bit bigger, maybe half a centimetre for seam allowance to make it easier to attach sides 1 and 2. I will also leave more room outside the hand to allow for errors such as this. I placed the Velostat on each finger, where I planned on positioning it and drew the outline in pencil.
Working with the material available to me, I had to make the sensors relatively small, I think to create a more inclusively interactive object the sensors should be longer, roughly 7CM.
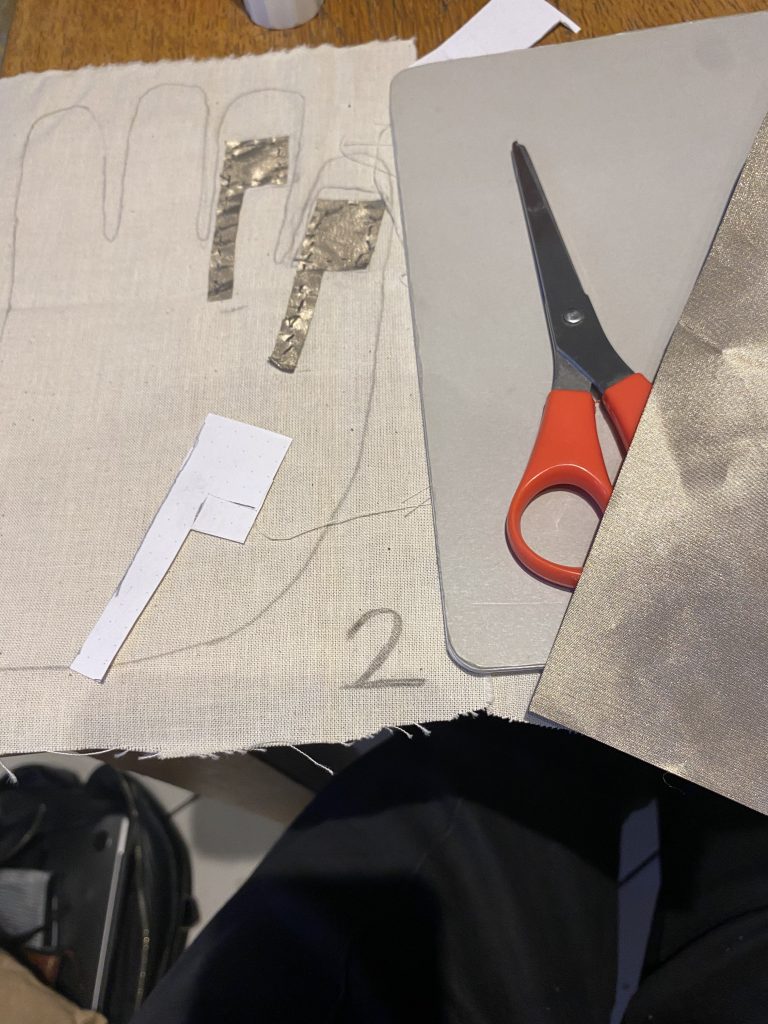
Making a template for the conductive fabric, ended up being very useful in cutting out uniform pieces of fabric. Measure twice cut once. When sewing the conductive fabric to each side it was difficult to make sure they were aligned on both sides without the long parts touching, I mostly did it by holding a light behind the fabric to check that they were placed right and then pinning them in place, I think by creating templates that indicate where the fabric is going to be placed will be helpful in future.
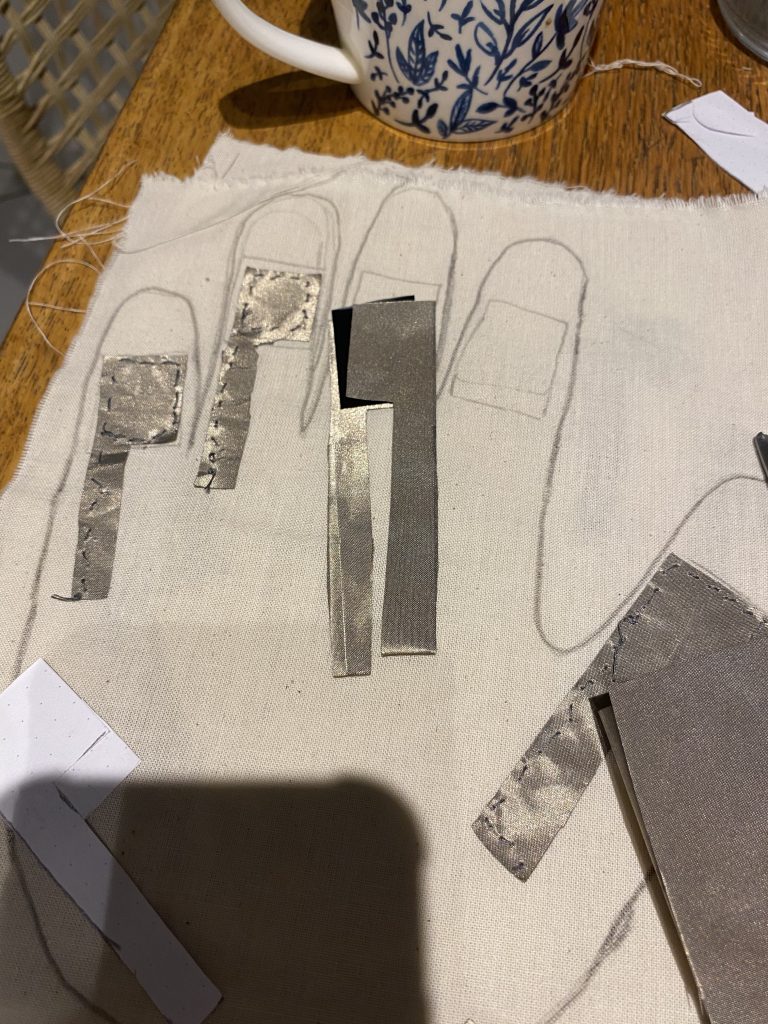
Checking the conductive fabric and Velostat cutouts are the right shape/ size.
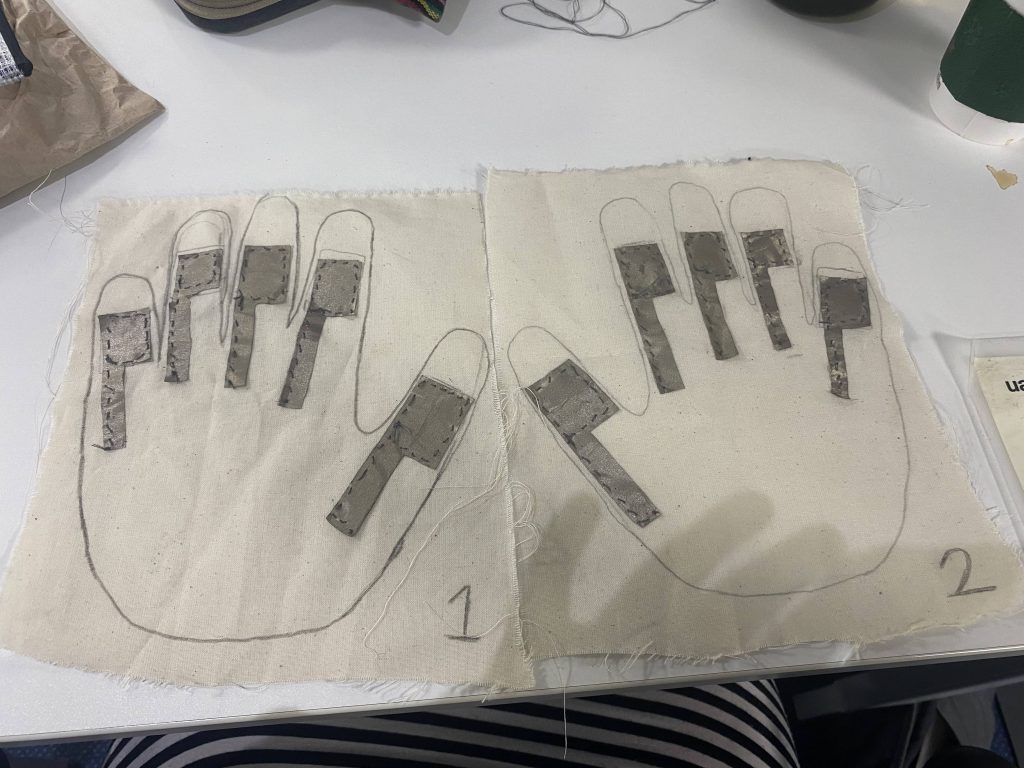
After I had sewn all the conductive fabric to both sides, I checked again that both the pads for each finger (one on side one, one on side two) aligned without having the long parts touching (I believe this would create a short circuit).
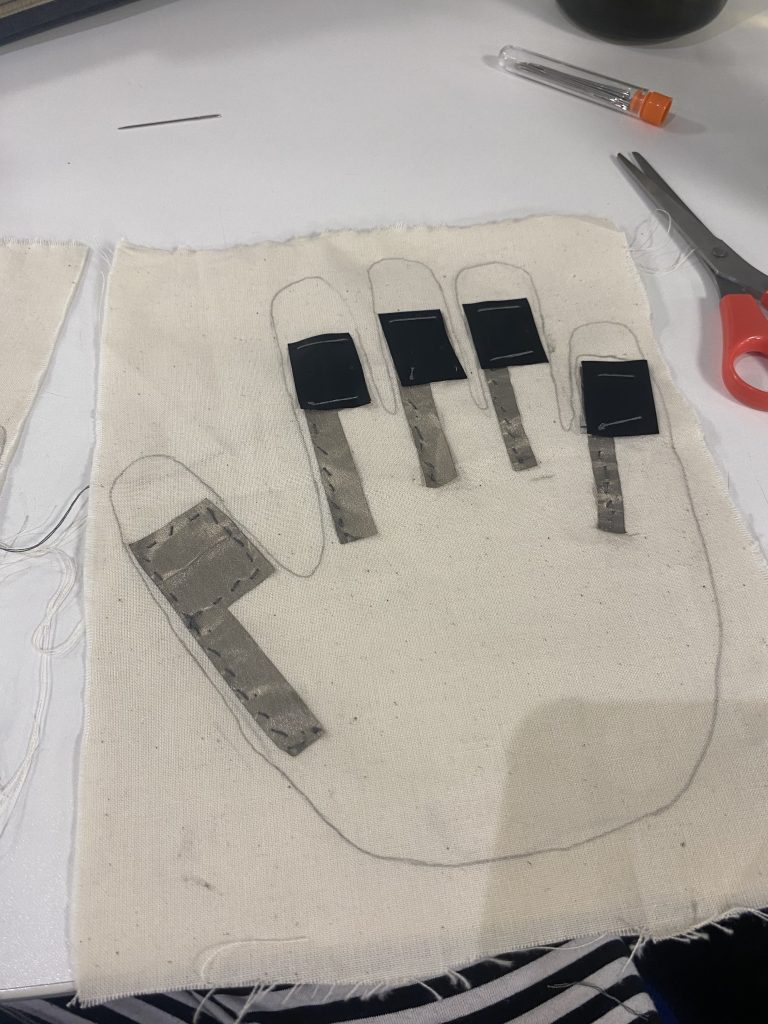
I sewed the Velostat to each finger on side two but mismeasured the conductive fabric on the thumb so have to wait to attach the Velostat there. MEASURE TWICE CUT ONCE!
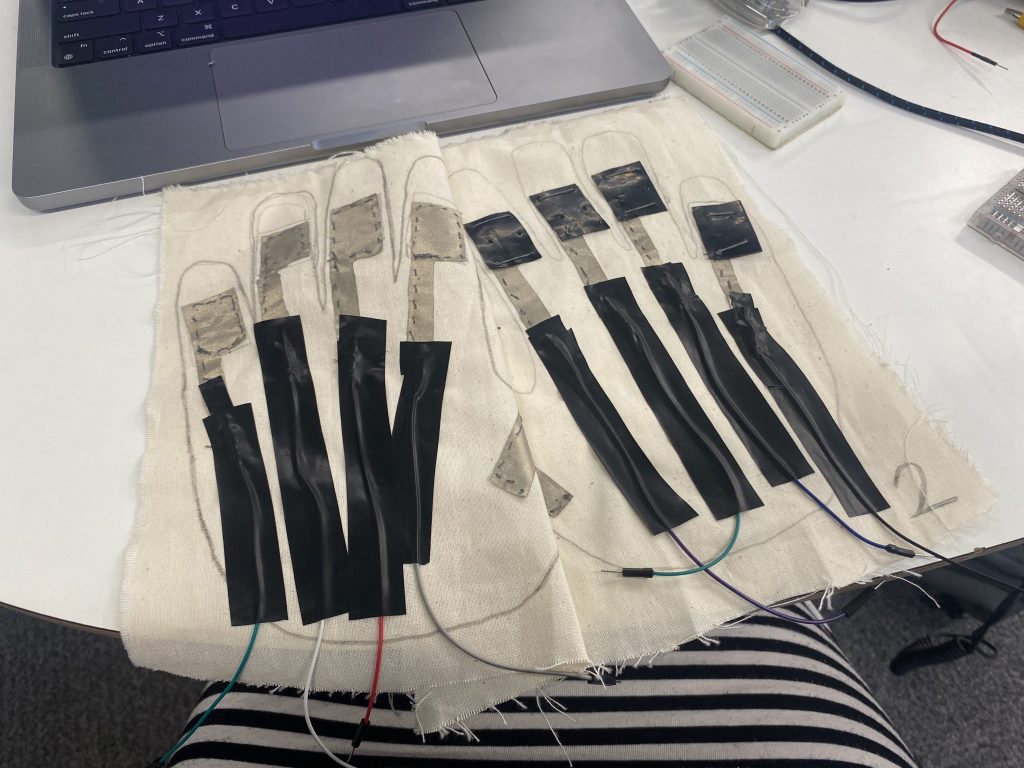
Attaching my E-textiles to hardware hasn’t been an obvious choice, I still feel uncertain as to how I will be permanently attaching wires to the conductive material. For a temporary solution, as this is a prototype I used jump wires and electrical tape, this seemed to work but proved to be an impermanent solution as when I went back to a day later the connections were fragile. I worry that if I solder the wire to the conductive material it will melt, I guess there is potential for other fastening methods such as hot glue or sewing? To be explored later.
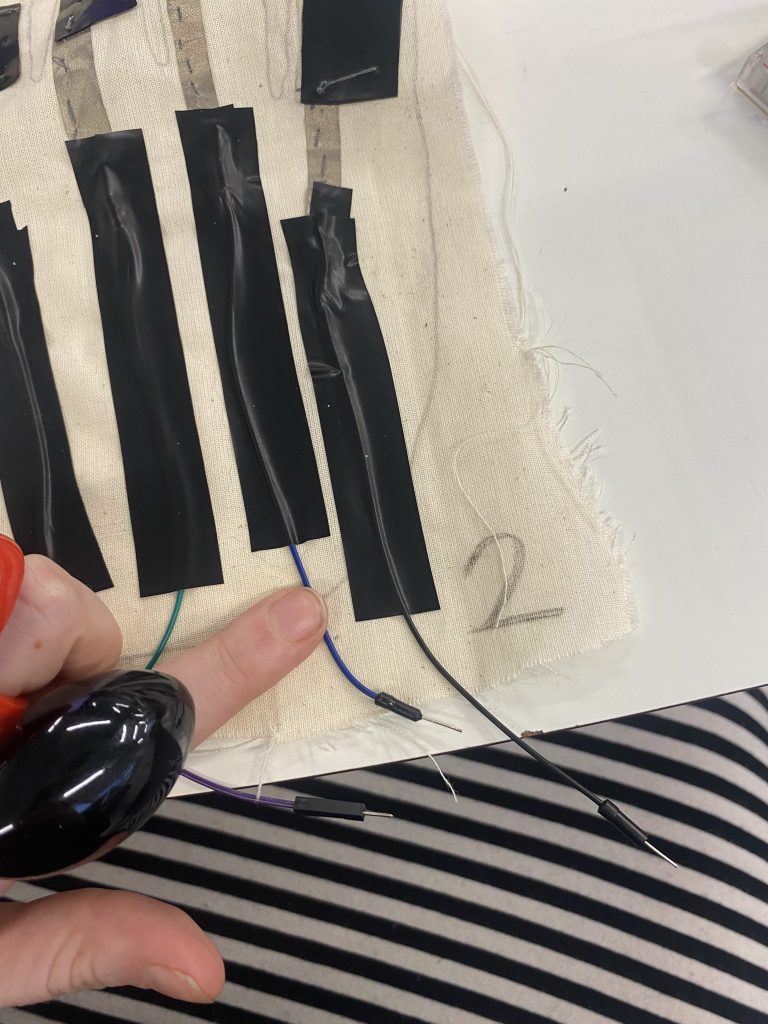
When taping the wires the first time, I did not consider that the length of wire is very important. There must be enough wire that the end being attached to the breadboard has enough room to attach. Now all wires attached to the sensor are approx 15CM. Ideally, I will change all wires to be 30CM in length, this will allow more options when placing the breadboard.
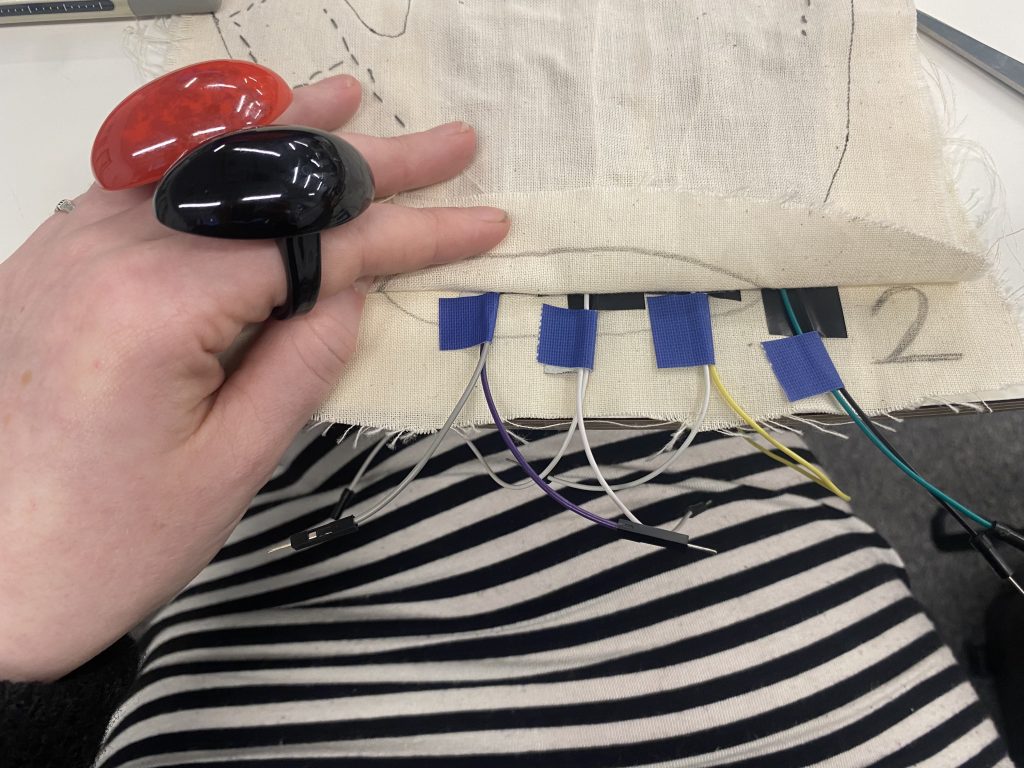
Taping the left and right wires for each sensor together so I know I’m using the right wire for each sensor.
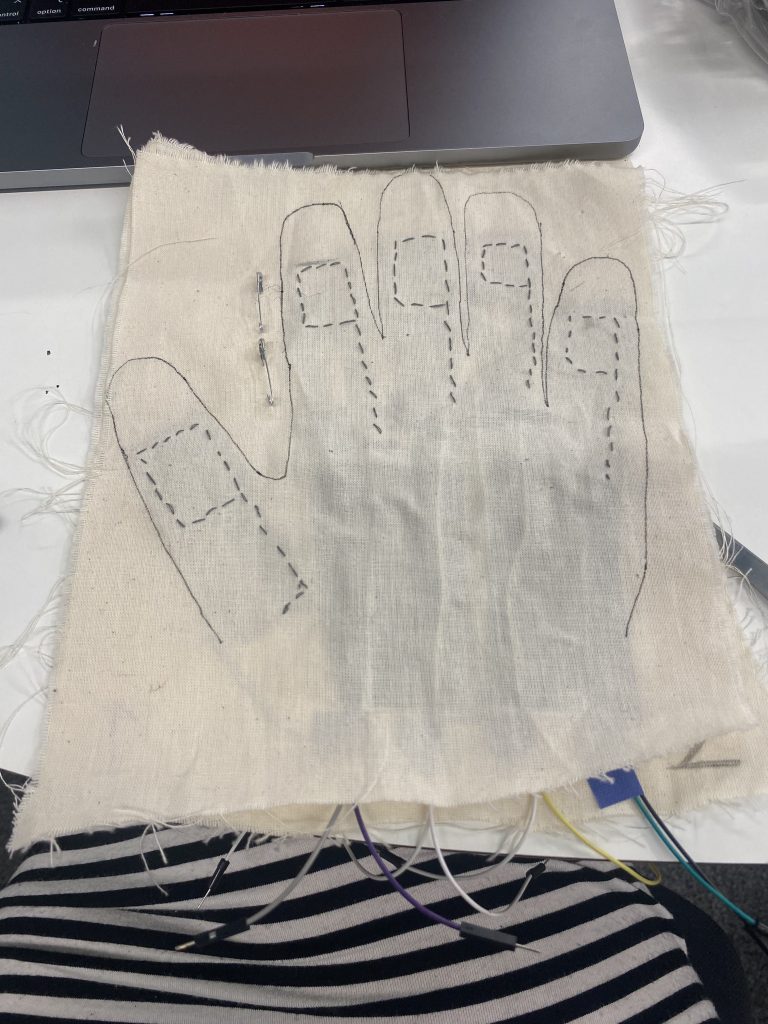
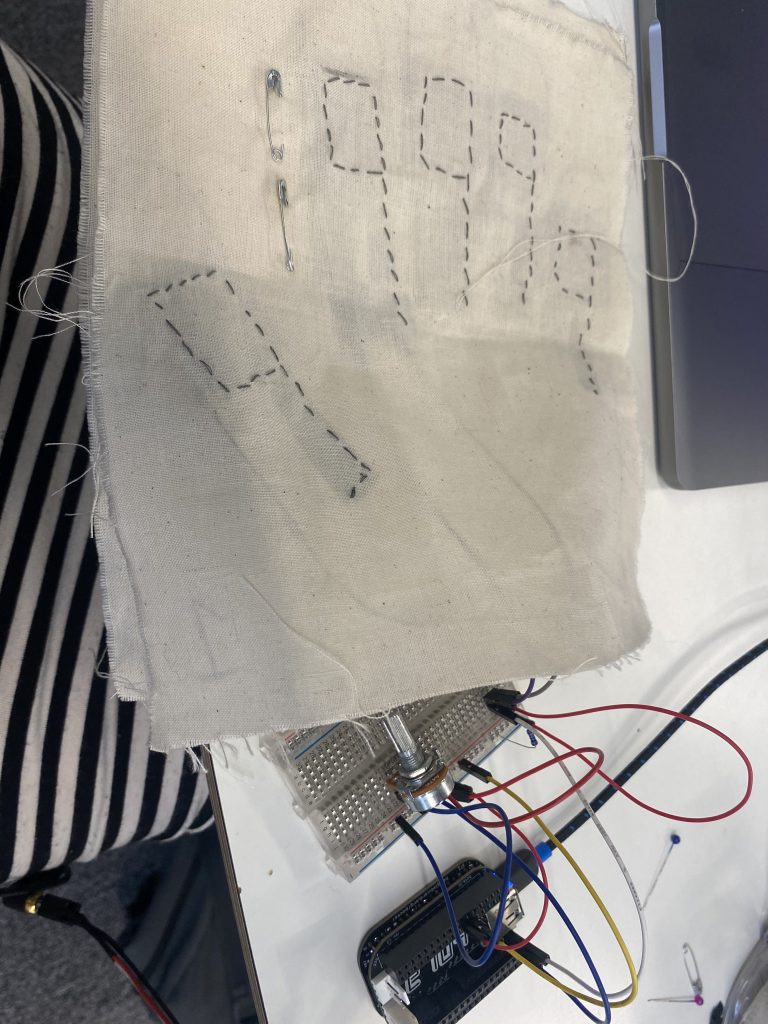
I really enjoy the aesthetics of the prototype. The stitching has accidentally made shapes that look like ‘9’. I safety pinned sides 1 and 2 together, as an impermanent way of attaching both sides which I also like the visual off. There could be some aesthetic interest and purpose in leaving the wires exposed, representing the relationship between the body and technology.
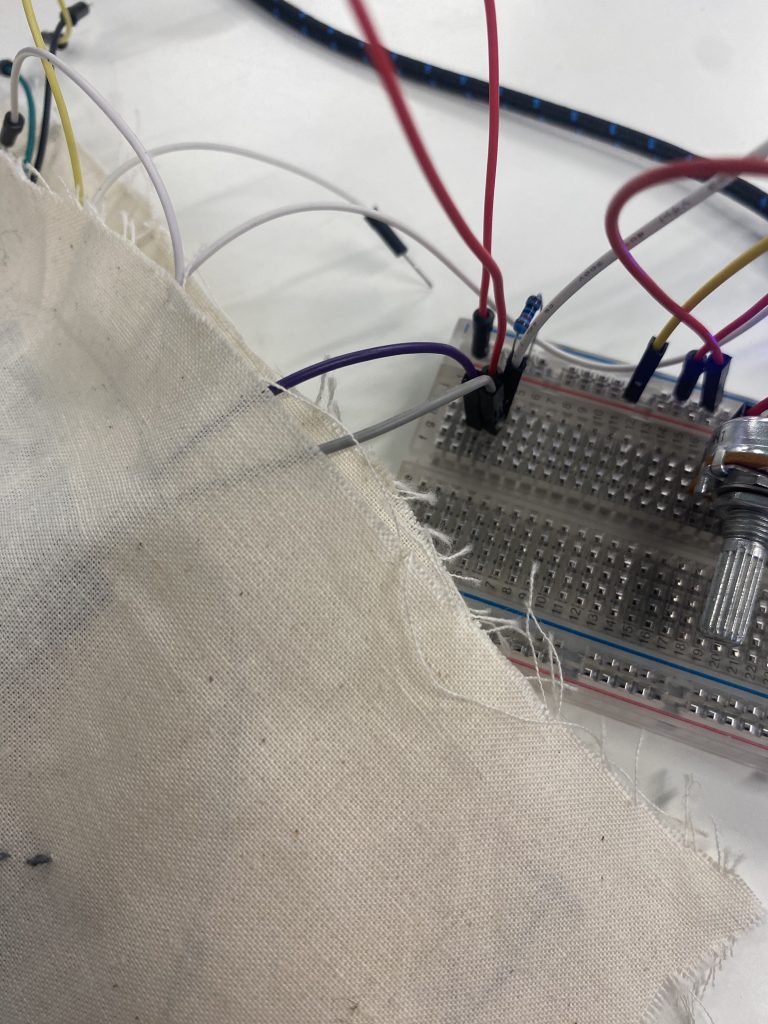
To test if all sensors work, including the wires, I used the Puredata patch (image below) that I know works with 1 sensor and tried the sensor individually. By doing this I could test that there were no short circuits and that the sensors definitely work.
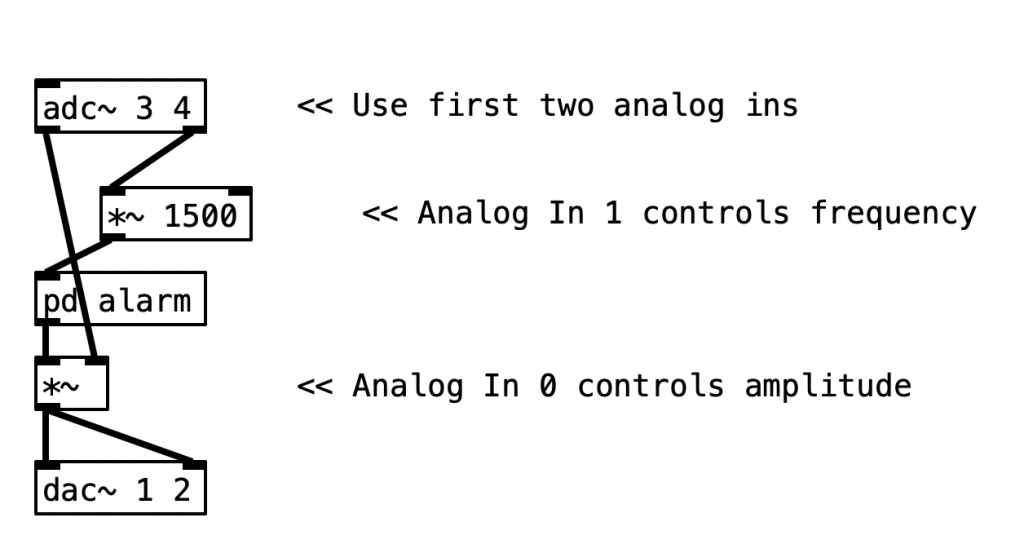